Custom Mold Design
Tailored solutions for your unique manufacturing needs.
11/15/20243 min read
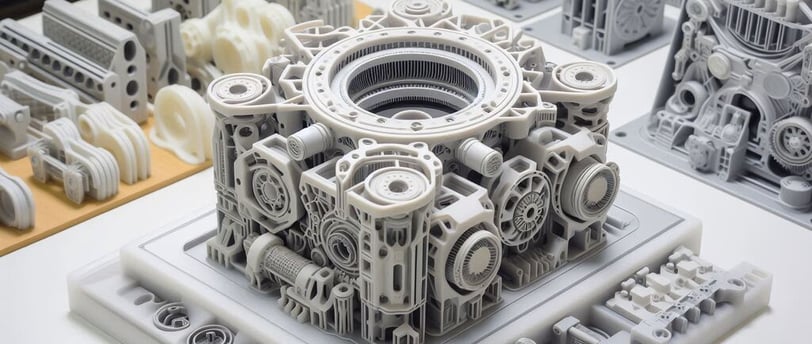
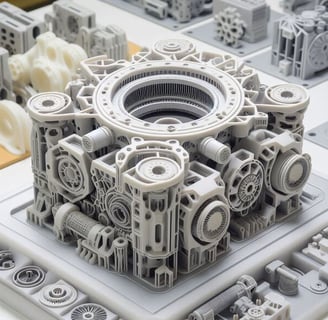
Custom Mold Design: Tailored Solutions for Your Unique Manufacturing Needs
In the ever-evolving world of manufacturing, efficiency and precision are paramount. Whether you’re producing consumer goods, automotive parts, or medical equipment, custom mold design can be the key to meeting your unique production needs. By tailoring molds to specific product requirements, manufacturers can ensure optimal quality, reduce costs, and improve efficiency.
What Is Custom Mold Design?
At its core, custom mold design is the process of creating molds specifically tailored to the dimensions, functionality, and materials of your product. Unlike generic molds, custom designs cater to unique specifications, ensuring the production of parts or components with unmatched precision.
Why Custom Mold Design Matters
Precision and Consistency
Tailored molds minimize errors, producing components that meet exact specifications every time.Material Optimization
Custom designs take into account the properties of your chosen materials, ensuring durability and performance.Cost Efficiency
By reducing material waste and avoiding costly errors, custom molds can save significant money over time.
Benefits of Custom Mold Design for Manufacturing
1. Enhanced Product Quality
Custom molds ensure that every detail, no matter how intricate, is captured. This leads to superior end products with high durability and flawless finishes.
Example: In the medical industry, precise custom molds are essential for producing devices like prosthetics or surgical tools, where even minor inaccuracies can have serious implications.
2. Reduced Production Time
With molds designed to fit seamlessly into production workflows, custom designs streamline processes, cutting down on manufacturing timelines.
3. Flexibility for Innovation
Custom molds allow for creative freedom, enabling manufacturers to bring complex or innovative designs to life.
Stat to Consider: According to a survey by Deloitte, 45% of manufacturers reported that tailored tools, such as custom molds, directly contributed to innovation in product development.
Types of Custom Mold Design
1. Injection Molding
Best for high-volume production, injection molding is commonly used for creating plastic parts. Customization ensures the mold accounts for intricate details and precise dimensions.
2. Blow Molding
Used for hollow objects like bottles and containers, custom blow molds focus on achieving uniformity in shape and wall thickness.
3. Compression Molding
This method is ideal for large, durable parts, such as automotive components. Custom molds ensure material is distributed evenly, reducing defects.
The Process of Custom Mold Design
Creating a custom mold involves several steps to ensure it aligns perfectly with your product’s requirements.
Step 1: Concept and Design
Collaboration begins with understanding your product’s specifications. Advanced CAD software is typically used to create detailed designs.
Pro Tip: Share as much information as possible about your product, including material, size, and usage, to ensure the mold design meets your needs.
Step 2: Prototype Creation
Before committing to a full mold, a prototype is developed for testing. This allows for adjustments and ensures the design is functional.
Step 3: Final Mold Fabrication
Once the prototype is approved, the mold is fabricated using high-precision techniques such as CNC machining or 3D printing.
Step 4: Testing and Refinement
The mold is tested in real-world production scenarios to identify and resolve any issues.
Tips for Choosing the Right Custom Mold Designer
Experience and Expertise
Look for a designer with a proven track record in your industry.Technology and Tools
Ensure they use advanced tools and techniques like CAD software and CNC machining.Customer Support
Choose a partner who offers post-production support and is open to modifications if needed.
Example Company: Reputable firms like Protolabs specialize in custom mold solutions for diverse industries.
Common Mistakes to Avoid
Underestimating Costs
While custom molds require an upfront investment, they save money in the long run by reducing waste and errors.Rushing the Design Phase
Skipping thorough testing can lead to costly adjustments later.Ignoring Material Properties
Ensure the mold design accounts for the behavior of your chosen material under production conditions.
FAQs About Custom Mold Design
Q: How long does it take to create a custom mold?
A: The timeline varies depending on complexity but typically ranges from 4 to 12 weeks.
Q: Are custom molds only for large-scale production?
A: No. Custom molds can be cost-effective for small production runs, especially when precision is critical.
Conclusion: Unlock Your Manufacturing Potential
Custom mold design offers a tailored solution to meet your unique manufacturing needs. From improving product quality to reducing production times, the benefits are undeniable. By investing in custom molds, you’re not just optimizing production—you’re setting the foundation for long-term success.